مقدمه ای درباره بویلرها:
بشر از قرنها پیش به قدرت بخار پی برده بود ولی استفاده صنعتی از دیگهای بخار از سال 1712 میلادی توسط (ساوری و نیوکامن) با ساخت اولین دیگ بخار با پوشش سربی یا چوبی و با فشار کمی بالاتر از فشار اتمسفر آغاز گردید. در سال 1725 میلادی ( هیستک بویلر) با صفحات فولاد پرچ شده و با فشار نسبی (( مورد استفاده قرار گرفت.
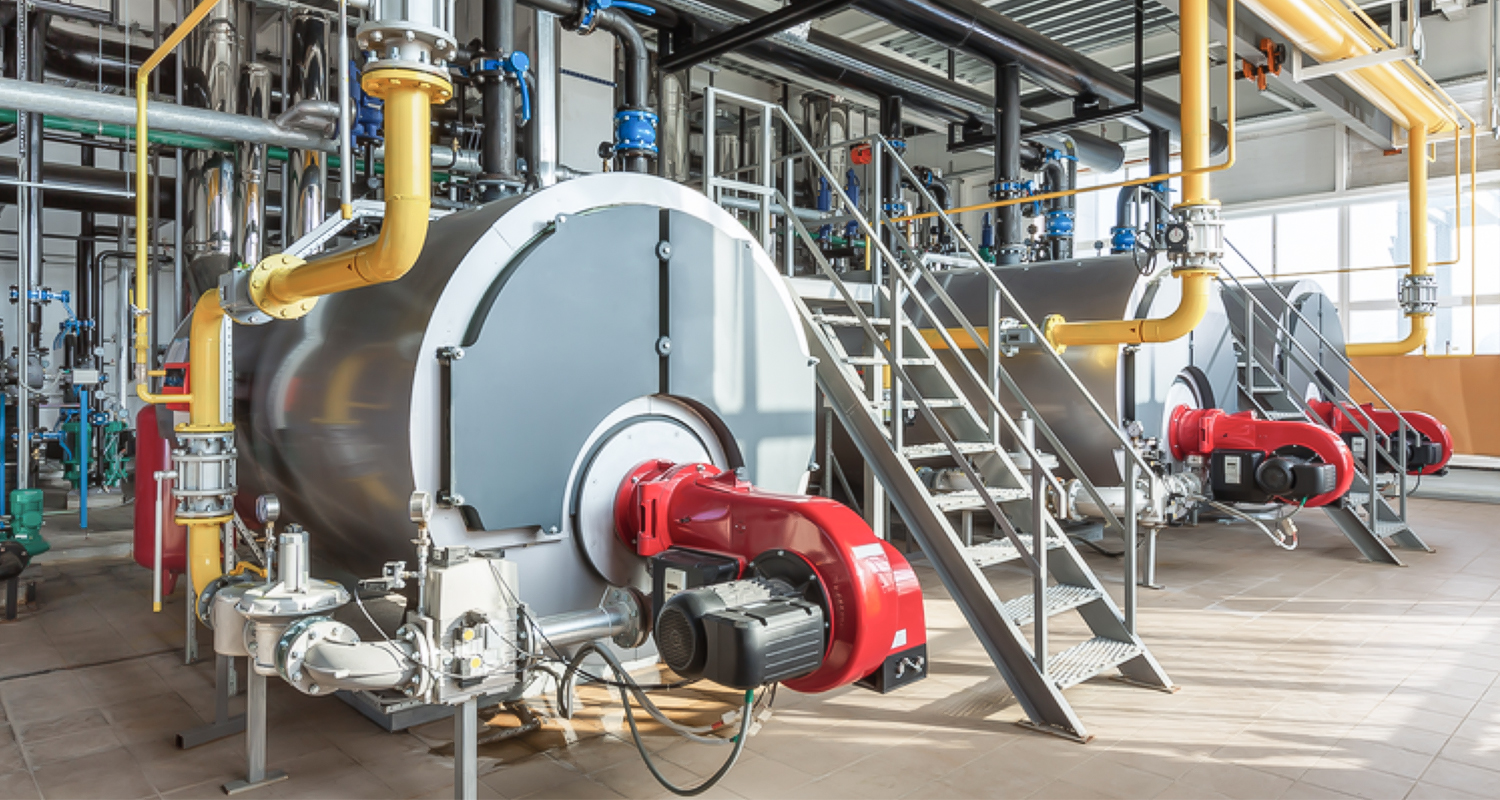
با گذشت زمان مشخص گردید که تنها شکل عملی استفاده از دیگ بخاری مدور ساختن آنهاست که در سال 1795 با بوجود آمدن صفحات نوردی دیگ بخار بصورت مدور ساخته شد. از سال 1873 دیگهای بخار بصورت لوله آبی (Water Tube) طراحی گردید(شکل-1). در لوله های مایل این نوع دیگ آب جریان پیدا کرده و توسط جداره لوله ها حرارت جذب می شود. با توجه به افزایش سطحی انتقال حرارت به بهترین وجه صورتمی گیرد.
با افزودن اجزایی چون سوپر هیتر، دی هیتر، اکونومایزر و گرمکنهای هوا و ... ، صورت اولیه دیگهای بخار به تدریج بصورت بویلرهای با ظرفیت بیشتر امروزی تبدیل شد.سیر پیشرفت و تکامل بویلر به صورت زیر بوده است:
1- افزایش درجه حرارت
2- افزایش فشار
3- افزایش تناژ بخار خروجی از بویلر
4- افزایش راندمان
5- سهولت کنترل
6-کاهش هزینه های ساخت، بهره برداری و تعمیرات
7-افزایش طول عمر بویلر
انواع بویلر:
وظیفه بویلر تبدیل مایع (آب) زیر اشباع به بخار فوق اشباع می باشدی ولی در صنعت به کلیه وسایل تولید بخار از مرحله مایع اشباع تا بخار سوپر هیت، بویلر گفته می شود.
بویلرها به واحدهای تولید بخار جهت مصارف همگانی، برق و مصارف صنعتی تقسیم می شوندکه بسته به نوع طراحی، می توانند سوخت هسته ای، ذغال سنگ، نفت کوره(مازوت) نفت گاز و گاز طبیعی مصرف کنند.
بویلرها بر اساس پارامترهای مختلف تقسیم بندی می شوند که بطور کلی عبارتند از:
بویلرها با سوخت هسته ای(راکتور)
استفاده از سوخت هسته ای برای تولید بخار فاقد عواقب نامطلوب سوخت فسیلی می باشد، ولی نیروگاههای هسته ای مقداری پرتو رادیو اکتیو در محیط آزاد می کنند که با این حال این امر قابل کنترل بوده و برای کارکرد عادی نیروگاههای هسته ای، مقدار این مواد بسیار پایینتر از حدی است که برای انسان و محیط زیان آور باشد. علاوه بر این نفت و گاز را می توان برای تولید مواد پتروشیمی و بسیاری از فراورده های صنعتی دیگر به کار برد و نباید این ماده را تنها بعنوان سوخت مصرف کرد. نیروگاههای هسته ای از راندمان بالایی برای تولید انرژی حرارتی برخوردارند. انرژی که می توان برای تولید برق از آن استفاده کرد. در تاسسیسات نیروگاههای هستهای، یک سیال ثانویه بین راکتور و بویلر جریان می یابد و در بویلر، حرارت از سیال ثانویه به آب منتقل میشود. بخار حاصل نیز در یک سیکل بخار معمولی جریان می یابد.
بویلرهای نیروگاههای هسته ای در انواع مختلف طراحی میگردند که مهمترین آنها راکتور آب سبک تحت فشار(راکتور آب جوشان-Boiling Water Reactor ) و راکتور با آب سنگین می باشد.
بویلرها با سوخت فسیلی:
در تمام بویلرهای صنعتی از سوخت فسیلی استفاده می شود. همچنین اکثر برق تولیدی در نیروگاههای کشورمان از سوخت فسیلی بخصوص مواد نفتی حاصل می گردد.
استفاده از سوخت فسیلی برای تولید برق، گازکربنیک زیادی تولید می کند. دلیل این امر آن است که مقدار گرمایی که از سوختن سوخت فسیلی حاصل می شود، بیش از سه برابر انرژی الکتریکی تولیدی است. مقدار گازکربنیکی که از نیروگاههای فسیلی آزاد می شود متناسب با مقدار گرمایی است که در اثر احتراق حاصل می شود. بنابر این تولید برق در نیروگاههای با سوخت فسیلی یکی از منابعی است که سبب تولید می شود.
با توجه به تاثیرات منفی سوخت فسیلی در زندگی بشر و محیط زیستی لازم است به هر وسیله ممکن در کاهش استفاده ازآن برای تولید برق اقدام شود. انواع بویلرهای فسیلی عبارتند از:
1-بویلرهای مخزنی:
این نوع بویلرها شامل یک مخزن سربسته می باشند که انتقال حرارت در خارج از آنها صورت گرفته و آب در داخل مخزن به بخار تبدیل می شود. راندمان بویلرهای مخزنی بسیار کم بوده و در حدود 30% است و فقط در مصارف صنعتی با میزان بخار کم استفاده می شوند.
2-بویلرها با لوله های آتش(Fire tube):
در این نوع بویلرها اطراف لوله ها از آب پوشانیده شده است و گازهای حاصل از احتراق از داخل لوله ها عبور کرده و انتقال حرارت مابین آب و محصولات انجام می گیرد. محفظه احتراق(کوره) می تواند در داخل یا در خارج بویلر قرار گیرد. راندمان بویلرهای Fire Tube حدود 70% می باشد که جهت تولید بخار در واحدهایی با ظرفیت و فشار کم بکار برده می شود.
3-بویلرها با لوله های آب جداری(Water Tube Boiler):
در انواع مختلف این نوع بویلرها(شکل-2)، انتقال حرارت بر اثر برخورد گازهای حاصل از احتراق با سطح خارجی لوله های محتوی آب و بخار به روشهای تشعشعی، جابجایی و هدایت صورت می گیرد.مزیت آنها نسبت به بویلرهای فایرتیوب، کم بودن قطر لوله های آب و بخار می باشد که باعث می شود تنشهای حرارتی کمتری به سطح لوله ها وارد شده و در نتیجه می توان این بویلرها را برای فشارها و ظرفیتهای بالا مورد استفاده قرار داد. راندمان این نوع بویلرها در حدود 85 الی 95 درصد می باشد.
2- بویلر با لوله های آب جداری
یک بویلر از نوع دیواره آبی شامل یک اتاق احتراق همراه لوله های آب، هدرها و درامهای بخار و آب می باشد. علاوه بر این اجزاء دارای سوپر هیترها, گرمکنهای هوا, اکونومایزر و نگهدارنده ها می باشد که همه اینها اجزاء بویلر را تشکیل می دهد.
در این نوع بویلر ها معمولا از لوله های عمودی دارای فین بصورت دیواره یکپارچه استفاده می شود. ساختمان این دیواره ها از یک سری لوله های عمودی تشکیل شده است که توسط جوش دادن یک نوار فلزی بنام Fin به هم متصل شده اند و دیواره ای پیوسته ایجاد می کنند. لوله های دیواره آبی از آنجاییکه تحت تاثیر شار حرارتی بسیار بالایی قرار دارند و از نوسانات فشار و درجه حرارت ,بخصوص هنگام راه اندازی از حالت سرد برخوردار میباشند, نیاز به طراحی دقیق دارند. معمولا لوله های آبی در محفظه احتراق بطور عمودی قرار می گیرند. این لولهها در بالا و پایین روی هدرها (Header) به قسمتهایی بنام Stub که تواما با هدر ساخته شده و یا در عمل به آن جوش داده می شوند, وصل شده اند. وجود هدر ها در بویلر از تعداد لوله هایی که مستقیما به درام(Drum) وصل می شوند, می کاهد. توزیع دما در لوله های دیوار آبی به عواملی نظیر ضریب انتقال حرارت جابجایی در داخل لوله ها, مقدار شار حرارتی در داخل محفظه احتراق, ضریب هدایت حرارتی و ابعاد و ساختار هندسی لوله و فین بستگی دارد. وجود فین باعث توزیع نسبی یکنواخت شار حرارتی در جداره داخلی لوله می گردد و افت حرارتی بویلر را کاهش می دهد. همچنین فینها سطح تبادل حرارت را افزایش داده سبب تبادل بیشتر حرارت میشوند.
3-1: بویلرهای یکبار گذر(فوق بحرانی)(Once Through Boiler):
بویلر های بدون درام که دارای فشار فوق بحرانی می باشند به بویلرهای بنسون معروفند. در این نوع بویلر طراحی مجموعه محوطه احتراق و لوله های دیواره ای به نحوی است که کلیه آب تغذیه کننده موجود در لوله های دیواره ای پس از طی محوطه احتراق و لوله های دیواره ای به بخار تبدیل شده و مستقیما به سمت سوپرهیترها هدایت می گردند, لذا این بویلرها بدون درام هستند. از آنجاییکه بویلرهای بنسون دارای فشار بالایی هستند, تکنولوژی پیشرفته ای برای ساخت آنها مورد نیاز است, ولی به علت عدم وجود درام, وزن کمتری نسبت به بویلرهای زیر فشار بحرانی (درام دار) دارند. در بویلرهای بنسون حجم مشخصی از آب تغذیه با یکبار گردش در بویلر باید به بخار تبدیل شود. به عبارت دیگر عدد سیرکولاسیون, یک می باشد. ولی از آنجا که این بویلرها بالای فشار بحرانی کار می کنند, برای افزایش طول لوله های دیواره ای, بر خلاف بویلرهای درام دار لوله ها را بصورت مورب در روی دیواره ها طراحی می کنند تا ارتفاع بویلر کاهش یابد.همچنین ضخامت لوله های دیوارهای به علت بالا بودن فشار, بیشتر از ضخامت لوله های بویلرهای درام دار است. در ابتدای راه اندازی بویلرهای بنسون برای جداسازی آب و بخار از هم از سیکلون استفاده می کنند که با استفاده از خاصیت گریز از مرکز, آب و بخار را از هم جدا می کند و در حالت کارکرد دائم بویلر, از مدار خارج می گردند. همچنین به علت پایین بودن عدد سیرکولاسیون کنترل آنها نسبت به بویلرهای درام دار دشوارتر است و به دلیل نداشتن درام در شرایط اضطراری ذخیره آب و بخار نخواهند داشت.
انواع مختلف بویلرهای مورد استفاده در صنعت:
1-هیترهای گازی غیر مستقیم(Indirect Heater):
ازنوع fire tube میباشند و یکی از موارد استفاده آنها گرم نمودن گاز طبیعی پس ازفشارشکن(گاز شهری) است.
2-هیترهای گازی مستقیم (Direct Heater):
که به کوره پالایشگاهی نیزمعروف بوده و از نوعWater Tubeهستند.لوله ها بطور مستقیم درمعرض شعله وحرارت هستند(تشعشع صورت می گیرد) و بخش کویل گونه که درمعرض انتقال حرارت جابجایی می باشند.
3-بویلرهای واکنش شیمیایی(راکتور):
بویلر بازیاب حرارتی (Recovery Boiler) واستوانه ای شکل می باشند که در مجتمع های پتروشیمی مورداستفاده قرار می گیرند و کویلهای حرارتی آنها بصورت مارپیچی در صفحه می باشند.
4-بویلرهای سیکل ترکیبی: (Heat Recovery Steam Generator)
این بویلرها از نوع بازیاب می باشند و جهت استفاده ازانرژی گازهای خروجی نیروگاه گازی(توربین گازی) استفاده میشوند(شکل-3). نیروگاه سیکل ترکیبی در واقع ترکیبی است بین نیروگاه بخار و توربین گاز جهت افزایش راندمان کلی سیستم، در این نوع، بخش توربین گاز می تواند از سیستم جدا شده و خود مستقل کار کند.
3- بویلر سیکل ترکیبی
5-بویلرهای بازیافت(Recovery Boiler):
که در بخش کوره های ذوب مورد استفاده قرار میگیرند. این بویلرها درمجتمع های ذوب فلزات درمسیر مستقیم مدار ذوب نصب می شوند وامکان جدایش آنها از سیستم در حال کار وجود ندارد.
6-بویلرهای زباله سوز:(Incinerator Boiler)
هدف اصلی ازبین بردن زباله های شهری و خانگی می باشد ضمن اینکه با این عمل برق نیز تولید میشود. این بویلرها به تجهیزات اضافی قبل و بعد از بویلر نیاز دارند(جهت انباشت زباله و تخلیه خاکستر).
7-بویلرهای ذغال سنگ سوز(Coal Boiler):
دراین بویلرها نیز به دلیل استفاده از ذغال سنگ به عنوان سوخت به تجهیزات جانبی قبل و پس از بویلر نیاز می باشد.
اجزاء بویلر:
هر بویلراز اجزاءگوناگونی تشکیل شده است که هرکدام جهت هدفی خاص دربویلرنصب می شوند. قسمتهای مختلف بویلر با توجه به نوع کارکرد به چند دسته کلی تقسیم می شوندکه عبارتند از:
اجزا تحت فشار(Pressure Part) :
به تمام قسمتهایی که از داخل آنها آب یا بخار عبور می کند(مثل لوله ها و هدرها)و فشار داخل آنها نسبت به محیط اطراف بسیار بیشتر است اجزاء تحت فشار می گویند(شکل-4). بطور کلی مسیر آب ازپمپ تغذیه آب بویلر (Boiler Feed Water) تا خروجی سوپرهیترها(Super Heater) به اجزاء تحت فشار معروفند که به ترتیب عبارتند از:
ý لوله اصلی تغذیه آب(Main Feed Water Pipe) :
انتقال دهنده آب از خروجی پمپ تغذیه بویلر تا هدر ورودی اکونومایزر می باشند.
ý هدر ورودی اکونومایزر (Economizer Inlet Header):
به طورکلی وظیفه هر هدر توزیع یا جمع نمودن سیال(آب یا بخار)می باشد.
الف) هدر توزیع کننده: اگر تعداد خروجی های هدرنسبت به ورودیهای آن بیشترباشد، هدرتوزیع کننده است. به عبارتی هدر ورودی می باشد.
ب) هدر جمع کننده: اگر تعداد ورودیهای هدرنسبت به خروجی های آن بیشتر باشدهدر از نوع جمع کننده یا هدر خروجی می باشد.
4- اجزا تحت فشار بویلر(بویلر نوع SC)
ý لوله های اکونومایزر(Economizer tube) :
هدف از ساخت اکونومایزر افزایش راندمان بویلر می باشد. زیرا هرچه میزان جذب انرژی گرمایی حاصل از گازهای احتراق توسط آب بیشترباشد موجب می شود که راندمان بویلر نیز افزایش یابد چرا که حداکثر راندمان حرارتی چیزی جز حداکثر انتقال حرارت بین دو سیال سرد و گرم نیست. به عبارت دیگر وظیفه اکونومایزر افزایش درجه حرارت آب ورودی تا نزدیکی دمایاشباع (حدود کمتر از دمای اشباع آب) می باشد و موجب جلوگیری از کاهش دمای آب موجود در درام می شود و نیز محل نصب آن درمحل خروجی گازهای حاصل از احتراق است.
جهت انتقال حرارت بیشتر، به سطوح حرارتی زیادتری نیاز می باشد.لذا بدین علت است که لوله های اکونومایزر را بصورت فین دار می سازند(وجود فین دراطراف لوله سبب افزایش سطوح حرارتی میشوند).وجود یا عدم وجود فین در اطراف لوله های اکونومایزر بستگی به نوع سوخت مصرفی بویلر دارد. اگر سوخت مصرفی از نوع سوخت سبک باشد (مانند گاز طبیعی)از لوله های فین دار استفاده میشود زیرا افت فشار گازهای حاصل از این نوع سوخت کم می باشد. ولی اگرسوخت مصرفی از نوع سنگین (مانند مازوت) باشد از لوله های بدون فین در اکونومایزر استفاده می شود. بطور کلی اگر افت فشار گازهای حاصل از احتراق کم باشد لوله های اکونومایزر فین دار هستند در غیر این صورت بدون فین هستند.
آرایش لوله هایاکونومایزر به دو صورت است:
a) آرایش مربعی (Iin Line)
b) آرایش مثلثی (Stager)
ý هدرهای خروجی اکونومایزر (Economizer Outlet Header):
بعنوان جمع کننده آب از حلقه های اکونومایزر و هدایت آن به سمت درام بخار می باشد.
ý لوله های ارتباطی بین خروجی اکونومایزر و درام بخار (Economizer Outlet Pipe to Steam Drum):
آب راازخروجی اکونومایزر تا ورودی درام بخار انتقال می دهد.
ý درام بخار(Steam Drum) :
وظیفه درام جداسازی آب و بخار از یکدیگر می باشد. تجهیزاتی که توسط شرکتهای مختلف برای جداسازی بخار بکار می رود متفاوت بوده ولی اساس کار آنها یکی است. در کلیه این تجهیزات مخلوط آب و بخار وارد جداکننده آب و بخار (Separator) شده و با حرکت چرخشی که به سیال (آب و بخار)داده می شود بدلیل نیروی گریز از مرکز که ایجاد می شود و قطرات آب بعلت سنگینی وزن از بخار جدا می گردند. سپس بخار پس از عبور از صفحات خشک کننده(Drier) آخرین قطرات آب خود را نیز از دست داده و به سمت لوله های سوپر هیتر هدایت می شود و آب بدون ذرات بخار توسط لوله های پایین آورنده (Down Comer) به سمت لوله های دیوارهای (Water Wall) هدایت می شوند.
دومین وظیفه درام عمل نمودن به عنوان یک مخزن و ذخیرهای برای بویلر است. درام می تواند با ذخیره آب یا بخار در خود، در شرایط بحرانی بهره برداری از بویلر مقداری از نیازهای آب یا بخار را تامین نمایید. در درام تقسیم یکنواخت آب ورودی از اکونومایزر و تزریق بعضی از محلولهای شیمیایی به بویلر انجام می گیرد.از آنجا که فشار داخل درام زیاد است لذا آنرا به شکل استوانهای که از قوانین مخازن تحت فشار جدار ضخیم تبعیت میکند، طراحی مینمایند.
درام بخار از اجزاء مختلفی تشکیل شده است که به دو قسمت داخلی(Internal) و خارجی(External) تقسیم میشوند.ازآنجاییکه شرح وظایف هریک از اجزا درام بسیار گسترده است لذا فقط به اسامی اجزا اصلی آن اشاره میشود:
1-جدا کننده آب و بخار(Separator)
2-خشک کننده آب و بخار(Chevron Drier)
3-رطوبت گیر(Drier)
4-لوله های داخلی(Internal Pipe)
ý درام آب (Water Drum)یا درام پایین(Lower Drum) :
این درام در پایینترین قسمت بویلر قرار گرفته و به شکل یک مخزن استوانهای افقی میباشد و در حقیقت بصورت یک هدر عمل می کند. پس از جدا شدن آب و بخار دردرام، آب به سمت لوله های پایین رونده (Down Comer) هدایت شده و وارد درام پایین میگردد.وظیفه این درام تقسیم یکنواخت آب تغذیه به لوله های دیوارهها و Bank Tube میباشد.
ý Bank Tube
دستهای از لولهها هستند که درام بالا را به درام پایین وصل میکنند بطوریکه قسمتی از آنها به صورت Down Comer و قسمتی از آنها بصورت Riser عمل میکنند.
ý لولههای بدنه اصلی بویلر (لولههای دیوارهای)Water Wall Tube
در بویلرهای مدرن هر سه نوع انتقال حرارت جابجایی، هدایت و تشعشع صورت میگیرد.که حاصل آن تبدیل آب به بخار در لولههای دیوارهای است.در این بویلرها معمولا از لولههای عمودی بصورت دیوار یکپارچه استفاده میشود. آب درون لولهها با جذب انرژی حرارتی، عمل خنک کاری دیوارهها را نیز انجام میدهند. بین لولههای دیوارهای یک نوع نوار فلزی که به فین موسوم است، قرار داده شده است. این فینها رابط بین لولهها بوده که علاوه بر یکپارچه ساختن دیوارهها، لولههای بکار رفته در آن، خود دارای فین بوده و با کنار هم قرار دادن دیواره یکپارچه بوجود میآید.
نحوه ساختمان دیواره آبی بستگی به احتراق، شرایط بخار و اندازه بویلر دارد. ترکیب قرار گرفتن لولههای واتروال دربویلرهای مختلف به شرح زیر است:
a) لولههای ساده که در داخل بلوک قرار گرفتهاند و معمولا به آنها Boiling Wall میگویند.
b) لولههای ساده که نزدیک هم قرار گرفتهاند و بنام لولههای مماسی معروفند.
c) لولههای فین دار
نقش دیواره آبی درجذب حرارت مورد نیاز برای تولید بخار و مزایای فراوان لوله و فین در این فرآیند، عبارتند از:
o توزیع متعادل شار حرارتی در امتداد سطح داخلی لولهها
o وجود سطوح گسترده فین که باعث کاهش فلز لوله برای جذب حرارت میشود.
o عدم نشت محصولات احتراق به خارج از بویلر که علاوه بر کاهش آلودگی محیط بویلر، باعث میشود که از I.D. Fan با قدرت کمتری استفاده گردد.
o استحکام زیاددیوارهها و لولهها، که باعث میشود در اثر تنشهای حرارتی، دچار خمیدگی نشود.
o کاهش زمان نصب
o کاهش وزن دیوارهها و راه اندازی سادهتر بویلر
o به دلیل عدم تماس بین عایق کورهها و محصولات احتراق به عمر عایقها افزوده شده، و جنس آنها نیز ازلحاظ اقتصادی مناسبتر خواهد شد. علاوه بر هزینه، تعمیر و نگهداری نیزدر این زمینه کاهش مییابد.
o لولهها میتوانند به گونهای طراحی شوند که سرعت سیال داخل آن با میزان انتقال حرارت متناسب باشد.
از معایب این نوع دیوارهها، گران بودن تولید آنها، نیاز به تخصص زیاد جهت جوشکاری و اتصال لولهها به فین و پرهزینه بودن تعمیرات و تعویض قسمت آسیب دیده دیوار میباشد.
درلولههای دیوارهای همواره جریان آب در داخل لوله از پایین بطرف بالا میباشد. و هرچه آب بطرف بالا حرکت میکند حرارت بیشتری جذب نموده و در نتیجه بخار بیشتری تولید میگردد. در بویلرهای گردش طبیعی (Natural Circulation) این حرکت بصورت طبیعی و بواسطه اختلاف دانسیته آب و مخلوط آب و بخار در لوله پایین آورنده (Forced Circulation) با توجه به کم بودن اختلاف دانسیته برای چرخش آب از پمپهای گردش اجباری(Forced Circulation Pump) استفاده میکنند.
لازم به ذکر است که تمام آب خروجی از لوله به بخار تبدیل نمیشود بلکه درصدی از آن به بخار تبدیل میشود. این درصد بخار بستگی به عدد چرخش (Circulation Number) بویلر دارد. بطوریکه هرچه عدد چرخش بویلر کمتر باشد میزان درصد بخار خروجی از لولههای دیوارهای بیشتر است. پس میتوان بیان کرد:
عدد چرخش آب در بویلر=1/(درصد بخار خروجی از لولههای دیوارهها یا کیفیت بخار)
مثلا وقتیکه میگوییم عدد چرخش یک بویلر 4 است یعنی اینکه اگر یک کیلوگرم آب در بویلر به بخار تبدیل شود باید 4 بار در لولههای دیوارهای و Down Comer به حرکت درآید یا به عبارتی به ازای هر بار چرخش 25٪ آن به بخار تبدیل میشود.
برای بویلرهای درام دار عدد چرخش از3 الی 10 میباشد و در بویلرهای بدون درام 1 میباشد. با افزایش عدد چرخش حجم بویلر افزایش مییابد، زیرا کیفیت بخار کم شده و تعداد دفعات چرخش آب در بویلر برای تبدیل آب به بخار، بیشتر میشود. همچنین با افزایش عدد چرخش احتمال سوختن لولههای بویلر کم میگردد و بهرهبرداری مطمئن تر است.
ý لولههای بالابر(Riser Pipe):
وظیفه آنها بعنوان انتقال دهنده آب و بخار از هدرهای خروجی لولههای دیوارهای به درام میباشد. لذا میتوان گفت Riser Pipe واسطهای بین هدر دیواره ها ودرام بخار است. زیرا اگر لولههای دیوارهای بطور مستقیم به درام وصل شوند به دلیل کثرت تعداد آنها، تعداد سوراخهای ایجاد شده در روی سطح درام بسیار زیاد میشود که حاصل آن ساخت درام با ضخامت بسیار زیاد میشود. لذا برایجلوگیری ازاین پدیده، آب و بخار جاری در لولههای دیوارهای، ابتدا در هدرهای خروجی جمع آوری شده، سپس توسط چند لوله Riser که تعداد آنها نسبت به لولههای دیوارهای بسیار کمتر است به سمت درام هدایت میشود.
ý لولههای انتقال دهنده بخاراشباع(Saturated Steam Pipe) :
وظیفه آنها انتقال بخار از درام تاهدرورودی سوپرهیتر میباشد. بخاری که بعد ازدرام مجددا حرارت داده میشود بخار خشک نامیده میشود که اصطلاحا کیفیت آن 100٪ است.
ý سوپرهیتر(اولیه و ثانویه) و دی سوپرهیتر: (Primary & Secondary Super Heater and Desuperheater)
بخارخروجی از درام برای اینکه انرژی بیشتری داشته باشد باید از حرارت بالاتری برخوردار باشد که اصطلاحا به آن بخار خشک یا سوپرهیت میگویند. این عمل در داخل سوپرهیترها که از لولههای موازی تشکیل شدهاند و در مسیرگازهای داغ حاصل از احتراق قرار گرفتهاند، انجام میگیرد. این لولهها حرارت محصولات احتراق را به بخار درون خود منتقل میکنند.
بسته به نوع بویلرسوپرهیترها یک یا چند مرحلهای طراحی میشوند. سوپرهیترها اکثرا بالای محفظه احتراق قرار دارند و این حرارت را بیشتربه صورت تشعشع و مقداری بصورت جابجایی دریافت میکنند. یک قسمت دیگر بویلر در منطقه کنوکسیونی بویلر قرار دارد که حرارت بصورت جابجایی به آنجا منتقل میشود. بخار ابتدا وارد سوپرهیتر اولیه شده و پس از خروج از آن توسط دی سوپرهیتر از نظر درجه حرارت کنترل شده، سپس وارد سوپرهیتر ثانویه شده به سمت بیرون از بویلر هدایت میشود. لولههای سوپر هیتر به صورت افقی، آویزان و یا L شکل طراحی میگردند. توربینهائی که در درجه حرارت زیاد بخار کار میکنند بینهایت به تغییرات درجه حرارت سوپرهیترها حساس هستند و تغییرات زیاد درجه حرارت ممکن است سبب خرابی محور و پره های توربین گردد. در سوپرهیترهای تشعشعی در اثر افزایش بار بویلر درجه حرارت افت می کند ولی در سوپرهیترهای جابجائی برعکس میباشد زیرا جریان گازهای حاصل از احتراق به افزایش درجه حرارت باسرعت بیشتری نسبت به سرعت جریان بخار صورت میگیرد. پس سیستم کنترل دمای بخار سوپرهیت باید بتواند بین پایینترین و بالاترین مقداربار بویلر درجه حرارت لازم را ثابت نگه دارد. علت اینکه دی سوپرهیتر دوجداره است برای این است که از رسیدن آب اشباع به دیوارههای داغ لوله جلوگیری کندتا موجب شکسته شدن آن نشود. در بویلرهائی که درجه حرارت خروجی پایین است نیازی به سوپرهیتر نمیباشد.
ý ری هیتر(Reheater)
انرژی بخار هنگام خروج از توربین فشار قوی بعلت انجام کار افت پیدا میکند. برای جلوگیری از وجود رطوبت در طبقات فشار ضعیف توربین، باید انرژی بخارهای برگشتی از توربین فشار قوی را بالا برده، سپس به سمت توربین فشار متوسط هدایت نمود. این عمل توسط ری هیتر انجام میگیرد. ری هیترها همانند سوپرهیتر بوده و از لولههای افقی و موازی تشکیل شدهاند. این لولهها در مسیر محصولات احتراق قرار گرفته و حرارت گازهای داغ را به داخل خود منتقل میکنند. وجود ری هیتر بستگی به ظرفیت بویلر و نوع طراحی نیروگاه دارد. در بویلرهای با ظرفیت کم معمولا از ری هیتر استفاده نمیکنند ولی در بویلرهای با ظرفیت بالابرای افزایش راندمان حتما از ری هیتر استفاده میشود.معمولا ری هیتر به دو بخش اولیه و ثانویه و گاهی به چندین بخش تقسیم میشود. اجزا ری هیتر عبارتند از:
1) لوله سرد بازیاب
2) هدر ورودی ری هیتر
3) لولههای ری هیتر
4) هدر خروجی ری هیتر
5) لولههای گرم بازگشتی
ý لوله اصلی انتقال دهنده بخار(Main Steam Pipe):
بخار سوپرهیت را از هدر خروجی سوپرهیت ثانویه به سمت توربین یا مبدلهای حرارتی هدایت میکند.
ý پیش گرمکن هوا(Steam Air Heater):
هنگامیکه هوای محیط سرد میشود، ذرات آب موجود در هوا در حین برخورد با پرههای فن موجب یخ زدن آب روی پرههای فن میشوند و این سبب سنگین شدن و شکستن پرههای فن میشود. لذا برای جلوگیری از این امر، هوای ورودی به کوره یک هیتر که از نوع بخاری است گرم میشود.
ý ژونگستروم(Gas air heater):
برای جلوگیری از ورود هوا با درجه حرارت پایین به داخل کوره از ژونگستروم(شکل-5) استفاده میشود و لذا از آن برای گرم کردن هوای ورودی به کوره استفاده میشود و از آنجاییکه هر دو سیال گاز هستند و راندمان آن نیز کم است آن را به صورت دوار میسازند. بطوریکه نیمی از آن در قسمت سرد و نیمی دیگر آن در قسمت گرم (دود) قراردارد و با چرخش پرههای سرد و گرم موجب انتقال حرارت میشود.
5- پیش گرم کن هوا
ý کوره(Furnace):
کوره یا اتاق احتراق محفظهای است که عمل احتراق سوخت در آن انجام میگیرد و باعث میشود تا انرژی حرارتی ایجاد شده توسط احتراق سوخت بصورت تشعشع در فضای کوره و یا بصورت جابجایی در جریان گازهای داغ و هدایت از طریق فلز لولهها به آب تغذیه درون لولهها انتقال یابد. حاصل این تبادل حرارت، جذب انرژی حرارتی توسط آب داخل لولهها و تبدیل آن به بخار است.
ý مشعلها(Burners):
وظیفه مشعلها تبدیل انرژی شیمیایی سوخت به انرژی حرارتی است. برای یک احتراق مناسب لازم است که سوخت بصورت پودر درآمده، بطوریکه قطرات با یک توزیع یکنواخت بتوانند سریعتر تبخیر شوند. مشعلها علاوه بر پودرکردن سوخت و تبدیل آن بصورت ذرات ریز، برای تبخیر سریع سوخت و احتراق، حرکتی بین قطرات سوخت و هوا ایجاد میکنند. به عبارت دیگر یک اغتشاش کامل بین ذرات هوا و سوخت بوجود میآورند. این امر سبب میشود که مخلوط یکنواختی از هوا و سوخت در فضای احتراق بوجود آید.
ý G.R.F(Gas Recirculation Fan):
بخشی از گازهای حاصل از احتراق ا بخاطر کنترل Nox و افزایش راندمان حرارتی به هوای ورودی اضافه میشود. با استفاده از G.R.F. درصدی از محصولات احتراق خروجی ازدودکش را به داخل کوره میفرستیم و این محصولات احتراق مانند یک لایه سطح خارجی لولهها را میپوشانند و مانع جذب انرژی لولهها از طریق تشعشع میشود. زیاد شدن مولکولها در داخل کوره کنوکسیون را زیاد میکند. G.R.F. در دمای کم خیلی موثر است، زیرا جذب انرژی تشعشعی را کم میکند و در راهاندازی مانع Over Heat شدن سوپرهیت میشود.
کنترل دمای بخار خروجی از سوپرهیترها:
الف- استفاده از دی سوپرهیتر (آب اسپری):
با استفاده از آب اسپری بعد از سوپرهیتر اولیه دمای بخار سوپرهیتر ثانویه کاهش پیدا میکند که فرمان آن از دمای بخار خروجی گرفته میشود. وجود این سیستم برای بویلر لازم است چون سریع و قابل اطمینان است. این سیستم طوری طراحی میشودکه در بار نامی نیز مقداری آب اسپری وجود داشته باشد تا در صورتیکه در شرایط خاصی مثل دوده گرفتن لولهها، دما به مقدار نامی نرسد با کاهش آب اسپری دمای نامی ایجاد میشود.
ب - تغییر زاویه مشعلها:
با این کار مقدار انرژی آزاد شده در داخل کوره رادر ارتفاعهای متفاوت تغییر میتوان داد. چون در این حالت مقدار انرژی آزاد شده ثابت میماند. پس با پایین آمدن سر مشعل، میزان بخار تولیدی افزایش مییابد پس درجه حرارت بخارکم میشود.
ج - استفاده ازG.R.F :
در هنگام راهاندازی جهت کنترل دمای بخار، مقداری از گازهای خروجی توسط G.R.F. به داخل کوره فرستاده میشود.
بویلرهای زباله سوز:
افزایش روزافزون مقدار زباله، فضای کم برای جمعآوری و نامناسب بودن روشهای جمعآوری و نابودی این زبالهها سبب شد دانشمندان برای رهایی از زبالهها، فرآیند گرمایش در دمای بسیار بالا(پلاسمای گرمایی) را مناسب تشخیص دهند؛ روشی که در آن دما آنقدر بالا برده میشود که مواد قدرت مقاومت ندارند و تجزیه میشوند، که مواد حاصله بسیار سادهترند و خطرات مواد اولیه را ندارند، بعلاوه موادی که بصورت جامد باقی میمانند، در خاک نفوذ نمیکنند و اختلاف حجم بسیاری با مقدار اولیه دارند کما اینکه بعنوان مواد اولیه در صنعت قابل استفاده میباشند.
پلاسما:
پلاسما یکی از حالات ماده میباشد.پلاسمای ستارگان و در فضای رقیق بین آنها، 99٪ جهان اطراف را در بر گرفته است.کلمه Plasma ابتدا به گاز یونیزه شده توسط دکتر لانگ مویر، یک شیمیدان-فیزیکدان امریکایی در سال 1929 گفته شد. پلاسما شامل مجموعهای از اتمها، یونها و الکترونهایی است که آزادانه حرکت میکنند.انرژی برای جدا کردن الکترونها از اتمهای گاز لازم است تا پلاسما بوجود آید. انرژی میتواند از منابع متعدد باشد: حرارتی، الکتریکی یا نوری(ماوراء بنفش یا مریی لیزر). پلاسما توسط میدانهای مغناطیسی و الکتریکی تحت تاثیر قرار میگیرد و شتاب میگیرد که به آن این توانایی را میدهدتا گازی قابل کنترل و مورد استفاده باشد.
سیستم پلاسما برای دفع زباله:
همه سیستمهای پلاسما از 5 قسمت اصلی تشکیل میشوند:
1-قسمت تغذیه
2-قسمت محفظه احتراق
3-قسمت عمل و فرایند روی گاز خروجی
4-جمع آوری محصولات جامد
5-امکانات و تجهیزات جانبی
مواد زباله پس از ورود به محوطه وارد قسمت تغذیه میشود.درقسمت تغذیه با دبی ازپیش تعیین شده، مواد را به داخل کوره(محفظه فرایند) می ریزند. گاز پلاسما که توسط مشعلهایی در درون کوره به دمایی چند برابر دمای سطح خورشید رسیده است، تشعشع کرده(در اثر یونیزه شدنو جهشهای الکترونی) و گرما از طریق تشعشعی و سپس جابجایی به لایههای نزدیک مشعل زباله انتقال مییابد. تشعشع، همرفت و هدایت هرسه عوامل انتقال حرارت از پلاسما به لایههای زباله در محفظه فرآیند هستند. زباله به روش Pyrolysis (سوختن بدون حضور اکسیژن) تجزیه شده، به مواد ساده و اولیه تبدیل میشوند. گازهای تولید شده توسط خروجی گاز که در دیواره استوانه کوره است و باقیمانده جامد که مادهای شیشه مانند و فلزات هستند، از کف کوره خارج میشوند. گازهای خارج شده که قسمت عمده آن را هیدروژن و منوکسید کربن تشکیل میدهد، شامل گازهای اسیدیمانند H2 S و HCL و گاهی اوقات فلزات فرار است.
در تکنولوژی پلاسما، بر خلاف سوزاندن معمولی، هیچ اکسیژنی مصرف نمیشود و نیاز به مخازن اکسیژن نیست و منبع انرژی آن سوختهای فسیلی نیست. ارزش حرارتی حاصل از مشعل پلاسما 2 تا 3 برابر ارزش حرارتی حاصل از سوختهای فسیلی است.
تکنولوژی پلاسما برای بدست آوردن دماهای بسیار بالا در مواد ذوب شده قابل کنترل است. در این سیستم فلزات و مواد غیرآلی موجود در زبالهها فازهای مختلفی را تشکیل میدهند و قابل جداکردن هستند.
زمینه فعالیتهای بخش طراحی و مهندسی بویلر در شرکت صنایع آذرآب
- طراحی دیگهای بخار یکپارچه(Package) صنعتی و نیروگاهی لوله آبی با چرخش طبیعی(Natural Circulation Water Tube Boiler) از ظرفیت حدود T/Hr20 تولید بخار به بالا دامنه وسیع فشار ودرجه حرارت بخار طبق درخواست مشتری.
- قرارداد انتقال تکنولوژی با شرکت IHI ژاپن در زمینه دیگهای بخار لوله آبی با سیستم چرخش طبیعی و سوختهای گازی و مایع به شرح زیر:
- دیگهای بخار یکپارچه از ظرفیت حدود T/Hr20 تا حدود T/Hr100
- دیگهای بخار صنعتی از ظرفیت T/Hr50 تا حدود T/Hr350
- دیگهای بخار نیروگاهی از ظرفیت حدود T/Hr390 تا حدود T/Hr2200
- قرارداد انتقال تکنولوژی با شرکت Gadelius k.k در زمینه پیش گرمکنهای هوا از نوع Lungstorm.
- سیکل ترکیبی FW